Hey Developers & Testers!
So I realized I never really posted on my approach to putting the suit together, so here are some notes on what I did.
K-Ceptors
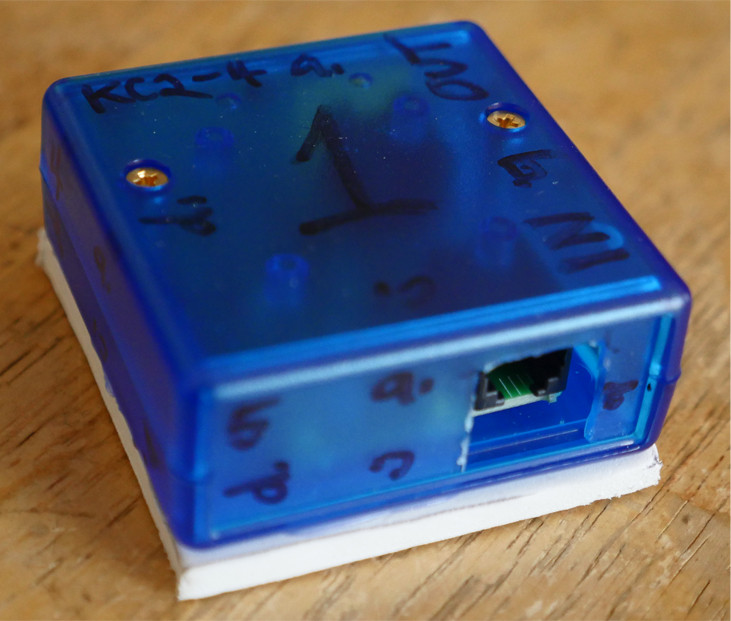
For the enclosure, I used this project box. If you want to get it from another vendor, this is a Hammond Manufacturing translucent blue plastic enclosure, Item#: 1593KTBU. This box fits the K-Ceptors perfectly, and if you want you can remove the sides covering the input/output. I opted to cut holes in each side instead, so I could put the calibration markings on all sides so I don't have to remove the K-Ceptor when I calibrate it. To keep the K-Ceptor securely mounted, but also avoid possible interference from ferrous metals, I've used all brass screws. The case is held together by 2 - 4-40 3/4 inch flat top screws with pointed tips.
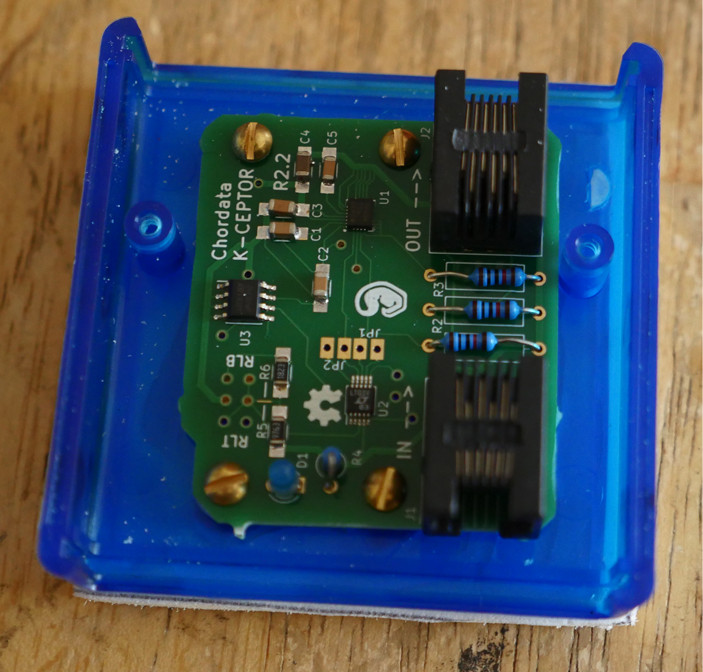
Inside, the K-Ceptor is mounted using 4 - 4-40 3/8 inch screws and 4 - 4-40 hex nuts.
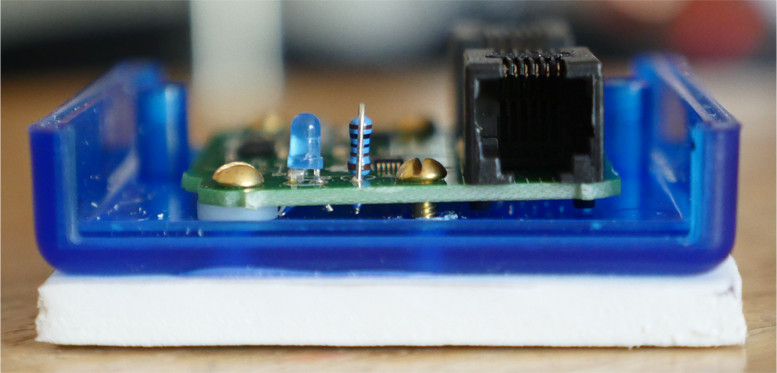
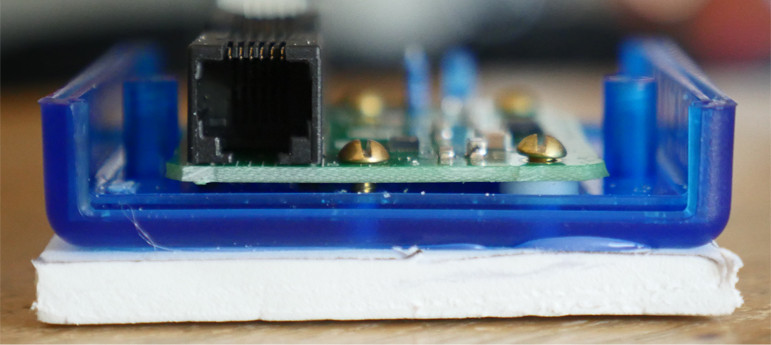
Also, to keep the K-Ceptors more or less level, I used 2 - #6 nylon flat washers.
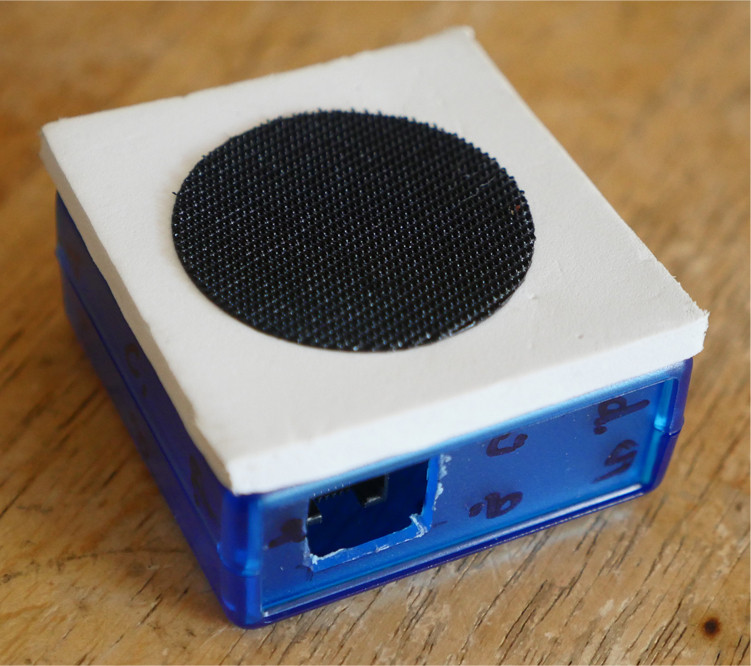
To prevent the hex nuts from coming loose, I used a sanding bit on a dremel to make 4 depressions in the foam (this was cut from 9x12 inch, 6mm thick foam sheet from Jo-Ann Frabrics under the Little Makers brand), and added hot glue to the depressions and the surface to affix the bottom part of the K-Ceptor box. Then I added velcro with adhesive backing the foam in order to attach them to the straps.
The Hub & Raspberry Pi
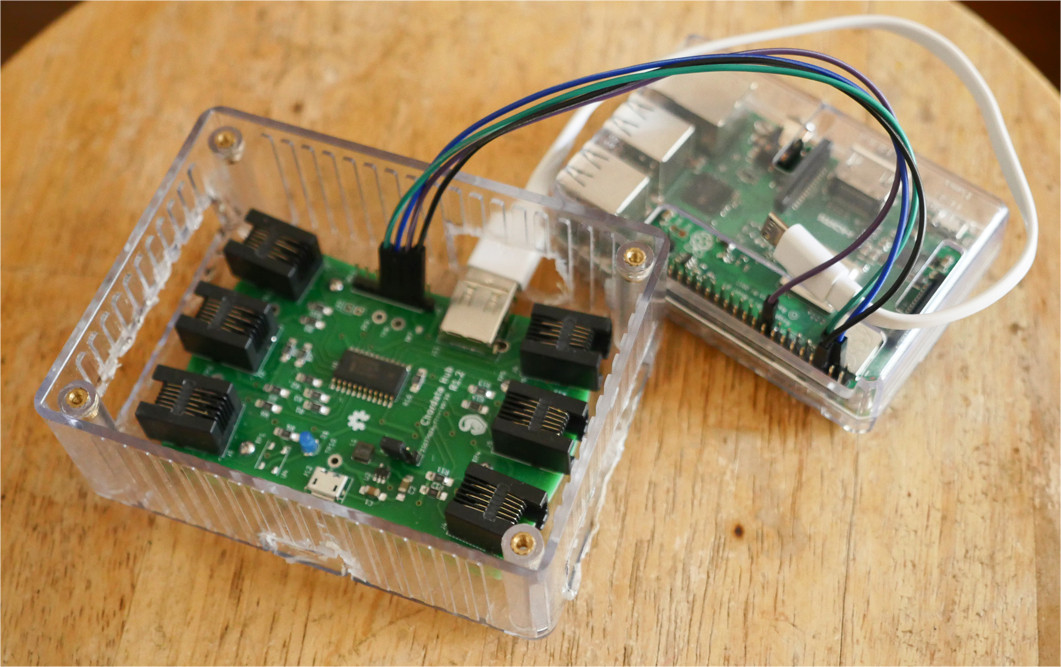
These parts have been a little problematic, in that I can't find a project box that fits both of them, but also fits into the belt pouch I purchased (Really, I just need Hub box to be just a little higher, but I haven't found such a box yet. So for now I just stack them like this when I put them in the pouch:
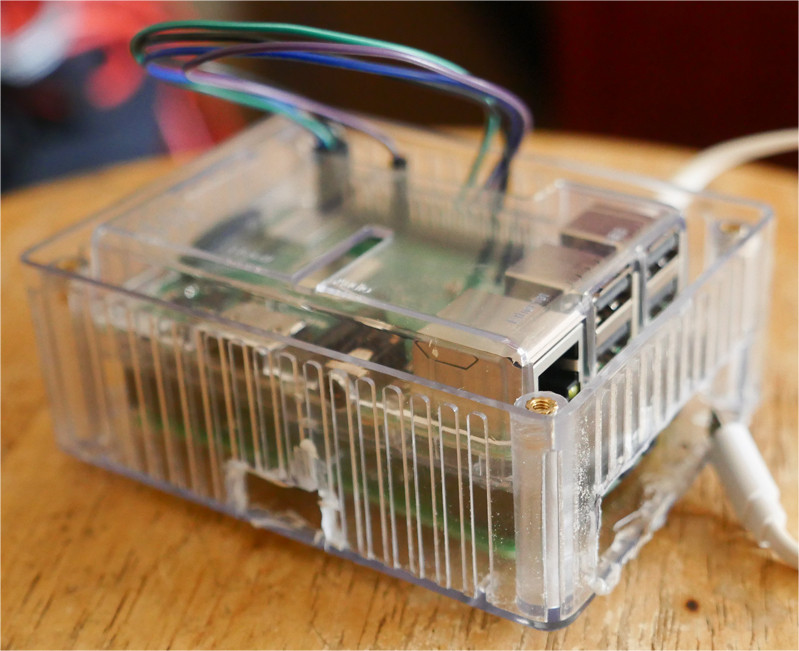
To mount the Hub to the box, I used 4 - 1-72 1/4-inch screws each with 1-72 hex nut, as you can see here:
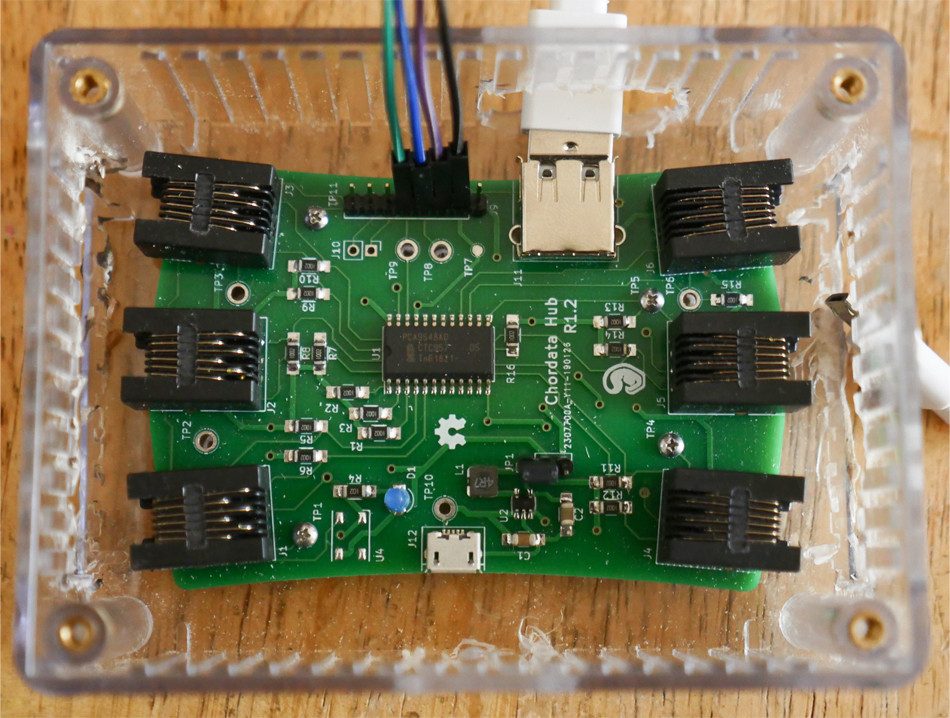
I might have a bit more to post on this later, but for now it's time to put together the new spine test rig and figure out what I'm doing wrong.